- Client: Nissan
- Sector: Industrial
- Size: 300 hectare
- Region: North East
- Services: McAlpine Design Group, Pre-Construction, Construction
- Completion Date: 1980
Evolving Nissan’s manufacturing site
Since constructing its original factory in the mid-1980s, we’ve worked closely with the car manufacturer as it has cemented its place in the European market.
With a design team located in an onsite office, we play an integral role, evolving facilities in line with strategy and productivity requirements.
Applying world-class engineering and cost-effective construction, we’ve expanded and updated production lines; built manufacturing for components and batteries; and created access roads and test tracks.
To date this amounts to more than 80 contracts completed at the Sunderland site.
And with factory outputs critical to success, these construction projects are delivered to exacting timelines without impacting factory operations.
Thanks to cutting-edge facilities - for manufacturing and assembly - the site is now the UK’s largest car manufacturer, employing more than 6,500 workers from the region.
The battery plant is pioneering and, as such, brought its challenges. It’s a very technical process with a building to match, but we’ve worked together to resolve a very complex project, managing the situation as a team to come up with the best solution.
Graham Bagley Nissan’s Head of UK Construction
Project summary
Our expertise
- Rapid delivery: Transforming the former airfield site into an 80,000m2 factory with 5km of roads took just 62 weeks.
- Electric avenue: We designed and built the highly technical and complex production plant for Nissan’s electric car batteries.
- Manufacturing efficiency: Originally, the factory made 12½ cars an hour. Thirty years later, a vehicle rolls off the plant line every 62 seconds.
- Driving regeneration: As well as employing more than 6,500 staff, 21,000 more people work in local companies supplying the factory.
- Integrated manufacturing: We’ve supported Nissan’s strategic move from assembling cars, to include manufacturing car components and batteries.
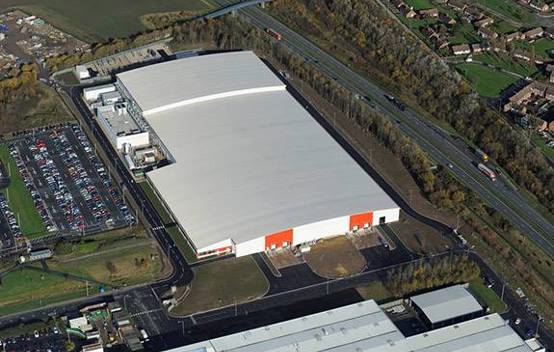
Complex requirements
We used Building Information Modelling to ensure the design of internal structures and secondary steelwork for the battery plant was carefully coordinated and integrated with M&E services and process engineering requirements.
Our site team worked to the stringent protocols required to deliver the plant’s demanding tolerances. This included laser screeding the floor and meeting the exacting specifications within the cleanroom/dryroom area.
The facility’s complex services and complicated build sequences required close collaboration with our specialist subcontractors to ensure all Nissan’s process entry dates were met.
Productive design
Effective design is critical in high-yield manufacturing, where a small alteration can make a big difference on output.
Working closely with their Nissan counterparts, our people have an in-depth understanding of the plant's processes. They workshop ideas with operatives, helping Nissan boost productivity through smart design and engineering.
Our in-house design group has been responsible for all the civil and structural engineering for our Nissan projects.
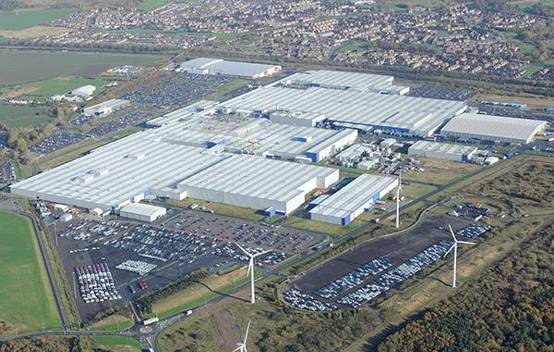
Industrial projects
-
McLaren Production Centre: Innovation meets efficiency
An example of industrial excellence displaying attention to detail and cutting-edge technology for a high-tech supercar manufacturing facility.
Sectors: IndustrialRegion: South East -
Project Inspire: Advancing defence infrastructure
Our team improved Defence Science & Technology Laboratory (DSTL)'s infrastructure by creating new office and lab facilities in Salisbury and Portsmouth as part of a rationalisation and relocation initiative.
Sectors: IndustrialRegion: South West -
'Thunderbird' Distribution Warehouse
Constructing one of the largest storage and distribution warehouses in the country while aspiring to retain all excavated materials on site.
Sectors: IndustrialRegion: Midlands