- Client: Mclaren Automotive
- Sector: Industrial
- Value: 85m
- Size: 32,000m2
- Region: South East
- Service: Construction
- Completion Date: 2012
McLaren Production Centre: Innovation meets efficiency
An example of industrial excellence displaying attention to detail and cutting-edge technology for a high-tech supercar manufacturing facility.
The McLaren Industrial Production Centre is a 32,000m2 high-tech sports car manufacturing facility located at McLaren Group’s Woking Headquarters in Surrey.
Delivered under a fast-track 12 month programme, meticulous attention to detail was essential to achieve the exacting standards required within what is a clinical production environment.
The building comprises a 12,000m2 basement and 20,000m2 ground floor featuring large open spaces with minimal columns. The centre is connected to the neighbouring McLaren Technology Centre via an 85m subterranean walkway.
Visitors enter through a glass rotunda containing a spiral walkway. This leads to a mezzanine level looking out over the 6m high production hall, the floor of which is covered with 200,000 porcelain tiles.
The McLaren Production Centre is as innovative and efficient as the cars that will be built inside it; made from the best materials, designed without waste or compromise, and operating in sympathy with the environment. It epitomises the forward thinking values of the McLaren Group.
RON DENNIS CBE MCLAREN GROUP CHAIRMAN AND CEO
Project summary
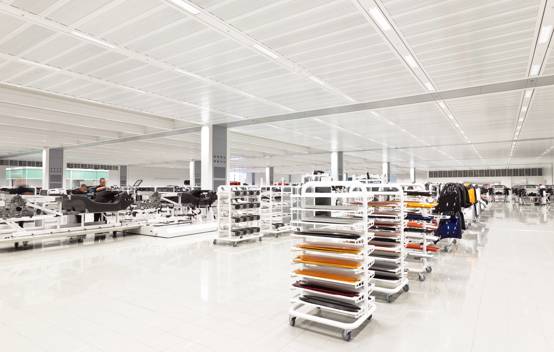
Outstanding attention to detail and clinical finishing
To deliver the precision finish required in this area of the building, the site was set out to a tiling grid which minimises the number of cut tiles.
This attention to detail applies right down to the tile joints lining up with the facilities in the washrooms, the door openings and the movement joints within the blockwork.
The interior of the building incorporates large areas of exposed concrete finished to the highest standards, white blockwork and Trimo paneling on the walls adding to the clinical feel.
Corporate responsibility
A 200,000m3 open cut excavation was required to sit the building into the surrounding landscape.
All the excavated material was retained and used to re-profile the site to the rear of the building.
68 mature trees were transplanted from the site into a nursery area to the rear of the development prior to the start of the bird nesting season.
A number of other trees were replanted on site to help screen the building from the road and Horsell Common respectively.
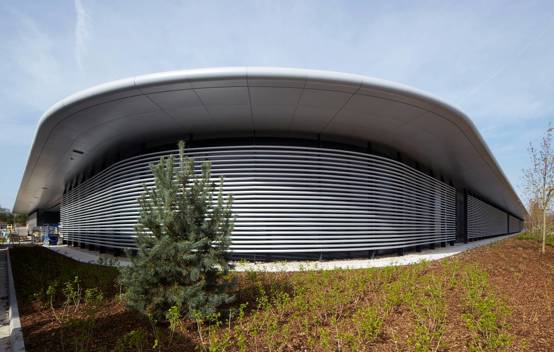
Industrial projects
-
Evolving Nissan’s manufacturing site
Since constructing its original factory in the mid-1980s, we’ve worked closely with the car manufacturer as it has cemented its place in the European market.
Sectors: IndustrialRegion: North East -
Project Inspire: Advancing defence infrastructure
Our team improved Defence Science & Technology Laboratory (DSTL)'s infrastructure by creating new office and lab facilities in Salisbury and Portsmouth as part of a rationalisation and relocation initiative.
Sectors: IndustrialRegion: South West -
'Thunderbird' Distribution Warehouse
Constructing one of the largest storage and distribution warehouses in the country while aspiring to retain all excavated materials on site.
Sectors: IndustrialRegion: Midlands