Built 125 years apart, the Glenfinnan and Colne Valley viaducts demonstrate that a passion for engineering excellence and a pioneering approach to construction remain our enduring trademarks.
Standing more than 30 metres high, the magnificent 21-arch Glenfinnan viaduct was constructed in the late 1890s and forms part of the 40-mile Fort William to Mallaig extension of the West Highland railway.
The numerous railway bridges and viaducts that punctuate the line were built in concrete; the first time the material had been used on this scale for such purposes.
Carving a route through the rugged terrain of the remote West Highlands with its bogs and ravines was hugely challenging and involved the construction of many cuttings and tunnels in mile after mile of unforgiving rock.
Fast forward 125 years and the company is again involved in one of the largest civil engineering projects in the country.
Stretching for more than two miles across the Colne Valley, the viaduct will be the longest railway bridge in the UK. It will carry the new high-speed line across a series of lakes and waterways on the north west outskirts of London.
We are undertaking the project as part of a joint venture called Align* delivering the Central 1 (C1) package for HS2 Phase 1, which also includes the two 10m diameter 16.2km Chiltern Tunnels.
Whilst constructed 125 years apart, in vastly different times and methods, in their vision and construction the two viaducts share a number of similarities. Both are monuments to their time. Colne Valley, with a design life of 120 years, is sleek, slender and elegant. Glenfinnan is described by the Scottish author JJ Bell, a staunch friend of the railway, as ‘a thing so delicate the fairies could have built it!’
The 1,250ft long Glenfinnan Viaduct features 21, 50ft wide arches built on an 800 feet (250m) radius. The curvature was achieved by tapering cross-sections of piers so that the inner face is shorter than the outer face. Only two pillars are hollow, to act as ‘stop’ piers and prevent progressive collapse in the event of an arch failure.
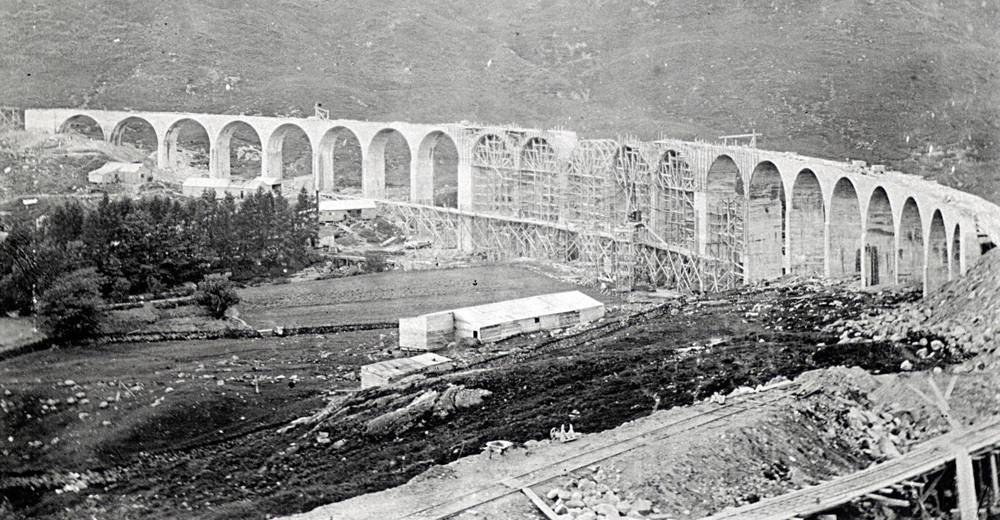
The 3.4km Colne Valley viaduct incorporates 56, 370 tonne cast in-situ concrete piers and 1,000 precast deck segments weighing up to 140 tonnes each. The segments are made at a purpose-built precast factory which has a production capacity of up to 15 segments per week.
To allow for the gentle curvature of the viaduct, all segments are a slightly different shape and produced using a cast-matching technique where each segment is cast against the previous one. This method ensures high accuracy, quality, safety and efficiency.
A 160m long launching girder assembles the deck segments to form the viaduct’s arches with each section post tensioned – steel tensioning cables are threaded through the segments to strengthen the structure. The segments are transported from the factory along the deck as it is built, reducing construction time, environmental impact and reducing construction traffic on local roads.
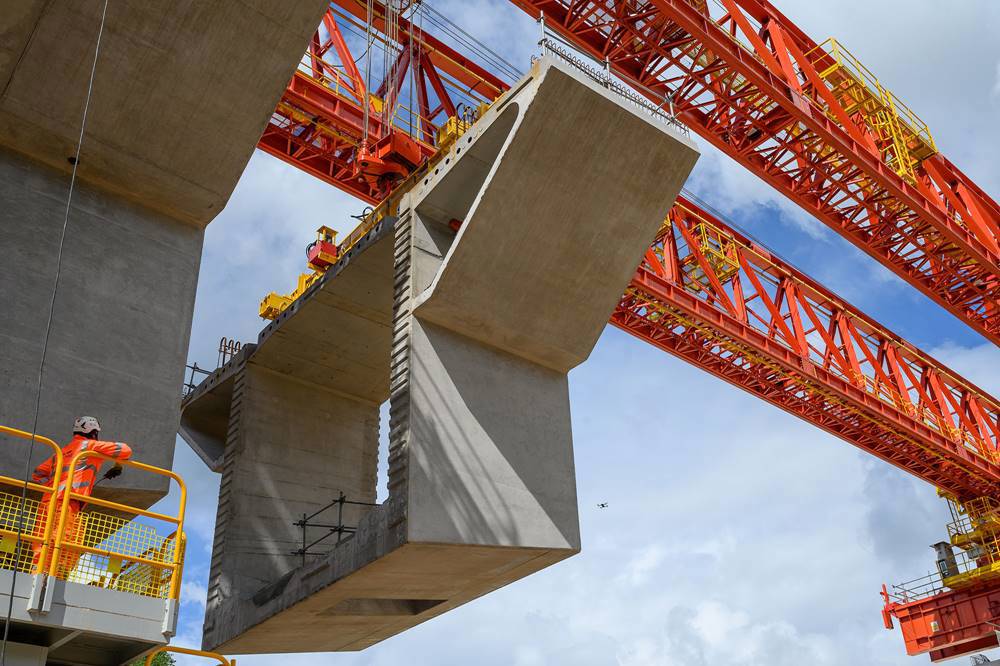
Glenfinnan was constructed entirely of mass concrete with an aggregate to cement mix of 4:1 for the abutments and bridge piers, which contained no sand. The stonebreakers’ screens were adjusted to provide the desired aggregate size. The nature of the rock used (mica-schist and gneiss) resulted in sharp, angular aggregate requiring care in compaction to achieve a satisfactory surface finish. It’s likely that this was mitigated by the cement-rich proportions used.
Formwork impressions on the underside of a Glenfinnan Viaduct arch.
At Colne Valley, the concrete mix designs incorporate 10 & 20mm crushed granite coarse aggregate with a blend of marine sea dredged sand and washed, crushed granite rock fines. Cement types CIIIA / CIIIB (1) includes 40%-70% GGBS1 for durability and ultimate strength, and a high cement content is used in the precast segments to achieve early age strength.
The precast mix design was developed and tested some 18 months prior to the first castings. High accelerator content and the use of heated aggregates and mixing water ensures the early age strength requirements (10.0MPa2 @ 10 hours & 20.0MPa (2) @ 20 hours) are achieved. A high flow workability consistency is required for placing and compaction within the mould. The initial setting time is 1.5 – 2.5 hours after batching. The precast team originally worked to a two-day cycle. As the process and prework on the concrete design has stabilised they’ve achieved a one-day cycle which is incorporated into the overarching programme.
Glenfinnan remains in use today and is testament to the quality of concrete and construction methods pioneered by Sir Robert. It has become world famous with railway enthusiasts and Harry Potter fans who flock to the viaduct to wave and cheer as the steam Jacobite crosses the valley.
We await to see how the world embraces its Colne Valley counterpart, but what is certain is that it is very unlikely that we will witness the construction of such a technically complex, aesthetically pleasing, concrete viaduct of this length again.
An unusual mix
The slender precast parapet units on the Colne Valley viaduct use a C150/165 (3) MPa UHPFRC (4) concrete mix. This is not well known in the UK and is possibly the largest current use of the material in the country today. It allows for reduced section thicknesses and a reduction in concrete volume and weight - providing a lower carbon footprint.
Through various carbon reduction initiatives, the project team had saved a total of 427,886 tonnes of CO2e as of March 2024. To put that into context, this equates to around 200,000 flights from London to Sydney!
- * Align JV = Bouygues Travaux Publics, a subsidiary of Bouygues Construction, Sir Robert McAlpine, and VolkerFitzpatrick, a subsidiary of VolkerWessels.
- (1) CIIIA / CIIB = A mix containing blast-furnace slag cement with 36% to 65% GGBS (Ground Granulated Blast-furnace Slag).
- (2) MPa = Mega Pascal, the unit for pressure (stress/strength).
- (3) C150/165 = Strength class.
- (4) UHPFRC = Ultra-High Performance Fiber-Reinforced Concrete.